Article of the Month -
September 2008
|
Review of Standards, Best Practice, Testing
and Calibration in Global Navigation Satellite System (GNSS)
Mr. David MARTIN, France
This article in .pdf-format (7
pages and 367 kB)
1) This paper has been prepared for
and presented at the FIG Working Week in Stockholm, Sweden 14-19 June
2008.
Key words: GNSS, standards, best practice, calibration.
SUMMARY
Surveyors as professionals must fulfil certain legal, regulatory
and/or accuracy requirements for their clients. Typically they will
strive to do this in an optimal cost effective way and with the most
appropriate equipment for the job at hand. Naturally it requires a good
understanding and assurance in the instrumentation employed. Clients
want the most from what they pay for. Legislative authorities as well as
private and public companies require confidence that the services
rendered are in conformity with globally accepted best practice rules.
Generally this involves the application of internationally recognized
standards.
Considerable efforts have been made concerning testing in the field
of surveying. In particular the ISO standard 17123 parts 1 through 8
concerning levels, theodolites, EDM’s, total stations and most recently
GNSS field measurement systems in real time kinematic (RTK); have been
published. Instrument manufacturers often quote these standards when
making reference to their instruments precision. Each of the ISO 17123
standards prescribes test procedures aimed at determining if the
instrument is functioning correctly and qualifying its precision and
performance.
This paper provides a general overview of standards, best practice,
testing and calibration related to GNSS.
1. INTRODUCTION
Surveyors as professionals must fulfil certain legal, regulatory
and/or accuracy requirements for their clients. Typically they will
strive to do this in an optimal cost effective way and with the most
appropriate equipment for the job at hand. Naturally it requires a good
understanding and assurance in the instrumentation employed.
Clients want the most from what they pay for. Legislative authorities
as well as private and public companies require confidence that the
services rendered are in conformity with globally accepted best practice
rules. Generally this involves the application of internationally
recognized standards.
Best practice is a management idea which asserts that there is a
technique or method that is more effective and efficient at delivering a
particular outcome than any other. It maintains that with proper
processes, checks, and testing, a desired outcome can be delivered with
fewer problems and unforeseen complications. Best practice is generally
based on repeatable procedures that have proven themselves over time for
large numbers of people. The notion of best practice does not commit
people or companies to one inflexible, unchanging practice. Instead, it
is an approach that encourages continuous learning and improvement. Best
practice in a field can be expected to evolve as new information,
instrumentation and methodology becomes available.
Best practice in surveying and GNSS in particular may have some very
job specific aspects associated with it. There may be legal and/or
legislative imperatives that do not impact directly on the measurement
process and thus strongly influence what may otherwise be regarded as
the best practice approach to the job. Nevertheless, and regardless of
the specificity of the job; an important objective in a survey is to get
the best possible results. This is typically synonymous with the highest
attainable precision. For the highest precision, it is generally
required to minimize errors. To minimize errors, it is imperative that
instrumentation is in proper working order. To ensure that an instrument
is fully functional, it is essential to test and/or calibrate it.
Considerable efforts have been made concerning survey instrument
testing. In particular the ISO standard 17123 parts 1 through 8 have
been published[1]. Instrument manufacturers often quote these standards
when making reference to their instruments precision. Each of the ISO
17123 standards prescribes test procedures aimed at determining: first
if the instrument is functioning correctly; and second, qualifying its
precision and performance. These tests should be made on a regular basis
2. STANDARDS
Few people question that their banking card works at every money
machine in the world, but this confidence could not be possible without
standards. While driving we stop at hexagonal, not round or
square-shaped stop signs. These are just two of the thousands of
standards that impact on our everyday lives.
A standard is a rule or requirement that is determined by a consensus
opinion of users and that prescribes the accepted and (theoretically)
the best criteria for a product, process, test, or procedure. The
general benefits of a standard are safety, quality, interchangeability
of parts or systems, and consistency across international borders.
ISO (International Organization for Standardization) is a global
network that identifies what International Standards are required by
business, government and society, develops them in partnership with the
sectors that will put them to use, adopts them by transparent procedures
based on national input and delivers them to be implemented
worldwide.[2]
The GIS/Geomatics profession is concerned by several series of ISO
standards. There are the ISO 12858 series concerning ancillary devices
for geodetic instruments; the ISO 17123 series field procedures for
testing geodetic and surveying instruments; and the ISO 191XX (6709,
19104, 19111, 19116, 19127, 19132, 19133, 19134, 19145) family
concerning standardization in the field of digital geographic
information. They aim to establish a structured set of standards for
information concerning objects or phenomena that are directly or
indirectly associated with a location relative to the Earth. Of
particular interest is ISO 19111 - Spatial referencing by coordinates
(i.e. geodesy). The FIG is very actively involved in standardization. A
good review of the merits of standardization in the field of surveying
is available on the FIG web page dedicated to this subject (http://www.fig.net/standards_network/index.htm).[3]
Another important standard that concerns the GIS/Geomatics profession
is the ISO 9000 family of standards. The ISO 9000 standards represent an
international consensus on good management practices aimed at ensuring
that a business or organization consistently delivers products or
services that meet the customer's quality and regulatory requirements
while aiming to enhance customer satisfaction, and continual improvement
in performance. These best practices have been distilled into a set of
standardized requirements for a quality management system (ISO
9001:2000). [4] They are applicable regardless of what the organization
does its size, or whether it's in the private, or public sector.
3. BEST PRACTICE
Best practice in GNSS is a broad field. Nevertheless, there are
several commonly accepted generic guidelines that can be regarded as
best practice to achieve optimal measurement results. These guidelines
typically aim to minimise the errors associated with GNSS measurements.
Listed below are several well known and common GNSS errors that
degrade the accuracy of derived coordinates in surveying applications:
- Multi-path and Electrical Interference,
- Obstructions,
- Ionospheric and Tropospheric influences,
- Incorrect Integer Ambiguity,
- Dilution of Precision (DOP) and Satellite Availability (SA),
- Inappropriately long Baseline Length,
- Lack of network redundancy,
- Use of poor quality or degraded benchmark and/or datum
references,
- Malfunctioning equipment,
- Blunders and human errors due to ignorance and bad survey
practice.
It should be noted that errors are often more likely to occur or to
be exacerbated in RTK surveys because of the relatively short occupation
times used.
Best practice in GNSS strives to avoid or minimise errors while
supplying appropriately documented measurements. This is done by
providing (legally) traceable measurements using an (inter)nationally
recognised reference network. Furthermore, equipment should be correctly
functioning and field tested (ISO 17123 part 8). Finally, properly
trained personnel prepared to confront the multiplicity of field
situations will always make the difference between a good or bad survey.
Typically a survey should be connected into several (at least 3)
stations in the reference network. They should become part of the survey
and should be used to constrain it. The level of agreement between
measured and reference values must conform to the precision required for
the survey, the GNSS technique employed and the client accuracy
specifications. For example, if one metre accuracy is required using
differential GNSS, then the measured and reference values should agree
to within 1 metre.
The connections to reference stations should be documented, outlining
the GNSS technique and reduction process, least squares adjustments, and
a comparison/analysis of the derived values. Archiving of raw
observation data and results files is highly recommended.
4. INSTRUMENT TESTING AND CALIBRATION
One common sense rule in the ISO 9001:2000 standard (chapter 7.6)
concerns the control of monitoring and measuring devices. Specifically
it requires that whenever necessary to ensure valid results, measuring
equipment shall be calibrated or verified at specified intervals, or
prior to use, against measurement standards traceable to international
or national measurement standards; where no such standards exist, the
basis used for calibration or verification shall be recorded.[4]
Surveyors have traditionally been very concerned about
instrumentation, its functionality and performance. At one time
instrument testing was second nature. Today, however with modern survey
instruments and their associated complexity, there is a tendency, due to
among other things the rapidity and simplicity of the measurement
process, to assume the measurements are exempt of error.[6] This of
course is not true.
Each of the ISO 17123 standards prescribes measurement procedures
aimed at qualifying an instrument precision and performance. They also
serve to verify if the instrument is in correct operating condition.
These tests should be made on a regular basis. For example field tests
can be made: at regular six month intervals; before and after a series
of precision measurements; after a long period of inactivity; and after
transport.[6]
Instrument testing (ISO 17123) should not be confused with an
instrument calibration. Calibration links the instrument directly to
international standards (see Figure 1 below). Calibration is the act of
checking or adjusting by comparison with a standard or reference the
accuracy of a measuring instrument. A standard or reference is an
instrument or method that will measure more accurately and precisely the
desired quantity than the measuring instrument itself. For example a
laser interferometer measures more accurate distances (relative
displacements) than a total station Electronic Distance Meter (EDM).
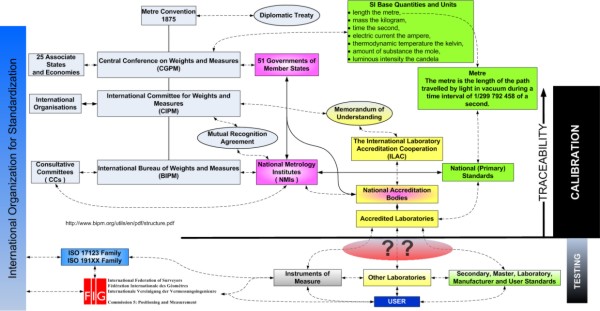
Figure 1. Structure of the notion of traceability, calibration
and testing of survey instruments.
One of the pillars of instrument calibration is the notion of
traceability. Indeed traceability is at the root of all legal metrology
and measurement. Traceability is a method of ensuring that a measurement
(even with its uncertainties) is an accurate representation of what it
is trying to measure. With traceability, it is possible to demonstrate
an unbroken chain of comparisons that ends at a national metrology
institute (NMI). Figure 1 above illustrates the links through the CGPM,
CIPM and BIPM to the NMI’s and Accreditation authorities to the user and
his/her instrument. Note that traceability is not assured if an
instrument is not linked through an accredited laboratory to a national
standard.
At present there is no consensus on GNSS calibration. This is because
it is complex field and there are differing, valid points of view
concerning what exactly needs to be calibrated and how to go about doing
it. Examples of different approaches are: anechoic chambers, baselines,
field testing facilities and robots. (see for example [5])
5. ISO 17123 PART 8: GNSS FIELD MEASUREMENT SYSTEMS IN REAL TIME
KINEMATIC (RTK)
This standard specifies field procedures to be adopted when
determining and evaluating the precision (repeatability) of Global
Navigation Satellite System (GNSS) field measurement systems (this
includes GPS, GLONASS as well as the future systems like GALILEO) in
real-time kinematic (GNSS RTK) and their ancillary equipment when used
in building, surveying and industrial measurements. Primarily, these
tests are intended to be field verifications of the suitability of a
particular instrument for the required application at hand, and to
satisfy the requirements of other standards. They are not proposed as
tests for acceptance or performance evaluations that are more
comprehensive in nature.
The results of the test are influenced by several factors, such as
satellite configuration visible at the points, ionospheric and
tropospheric conditions, multipath environment around the points,
precision of the equipment, quality of the software running in the rover
equipment or in the system generating the data transmitted from the base
point.
The test field consists of a base point and two rover points. The
location of the rover points must be close to the area and in time to
the task concerned. The separation of two rover points is between 2 m
and 20 m. The horizontal distance and height difference between two
rover points are determined by methods with precision better than 3 mm
other than RTK. These values are considered as nominal values and are
used simply to ensure that the GNSS measurements are free of outliers.
The standard proposes two tests: the simplified and the full test
procedures. The simplified test procedure consists of a single series of
measurements and provides an estimate of whether the precision of the
equipment is within a specified allowable deviation.
The simplified test procedure is based on a limited number of
measurements so a significant standard deviation cannot be obtained and
no statistical tests are applied.
The full test procedure is used to determine the equipments best
achievable measure of precision. It comprises three series of
measurements and is intended to determine the experimental standard
deviation for a single position and height measurement.
It may be used to determine:
- the measure of the precision of equipment under given conditions
(including typical short and long term influences);
- the measure of the precision of equipment used in different
periods of time or under different conditions (multiple samples);
- the measure of the capability of comparison between different
precision of equipment achievable under similar conditions.
- Statistical tests are applied to the test results.
6. SUMMARY
This paper has aimed to review standards, calibration, testing and
best practice in GNSS. It is necessarily brief. Nevertheless, no one can
doubt the importance of standards and best practice in the modern world.
Surveyors are becoming more and more involved in the standardization
process. This is clearly underpinned by importance standards have taken
on in geomatics profession and the FIG today.
One important aspect of standards is the periodic testing and
calibration of survey instruments. The ISO standard 17123 Optics and
Optical Instruments - Field Procedures for Testing Geodetic and
Surveying Instruments is concerned with survey instrument testing. In
particular part 8 of this standard GNSS field measurement systems in
real time kinematic (RTK) outlines a commonly accepted method to be
adopted when determining and evaluating the precision (repeatability) of
Global Navigation Satellite System (GNSS) field measurement systems
(this includes GPS, GLONASS as well as the future systems like GALILEO)
in real-time kinematic (GNSS RTK) and their ancillary equipment when
used in building, surveying and industrial measurements.
REFERENCES
- ISO, ISO 17123 Optics and optical instruments - Field procedures
for testing geodetic and surveying instruments Parts 1 to 8.
2001-2007, ISO: Geneva Switzerland.
- ISO, ISO in brief International Standards for a sustainable
world, I.O.f. Standardization, Editor. 2005, International
Organization for Standardization.
- Greenway, I., FIG Guide on Standardisation. 2006, FIG Task Force
on Standards.
- ISO, Quality management systems — Requirements. 2000:
International Organization for Standardization.
- Wübbena G., S.M., Mader G., Czopek F. GPS Block II/IIA Satellite
Antenna Testing using the Automated Absolute Field Calibration with
Robot. in ION GNSS 2007. 2007. Fort Worth, Texas, USA.
- Staiger, R., Le Contrôle des Instruments Géodésiques. XYZ Revue
de l'Association Français de Topographie, 2004. 99(2): p. 39-46.
BIOGRAPHICAL NOTES
David Martin is head of the ESRF Alignment and Geodesy Group.
He holds an MSc in Surveying from the Department of Geomatic
Engineering, University College London. He is the chair of FIG Working
Group 5.1 Standards, Quality Assurance and Calibration. He has published
a number of papers concerning accelerator alignment, survey instrument
calibration and hydrostatic levelling systems.
MORE TO READ
Powerpoint presentation at the FIG Working Week 2008 in Stockholm,
Sweden, June 2008:
http://www.fig.net/pub/fig2008/ppt/ts04c/ts04c_01_martin_ppt_2872.pdf
CONTACTS
David Martin
European Synchrotron Radiation Facility (ESRF)
6, rue Jules Horowitz
BP 220
F-38043 Grenoble Cedex 09
FRANCE
Tel. +33 (0)4 76 88 22 45
Fax +33 (0)4 76 88 23 13
Email: martin@esrf.fr
Web site: http://www.esrf.eu
 |